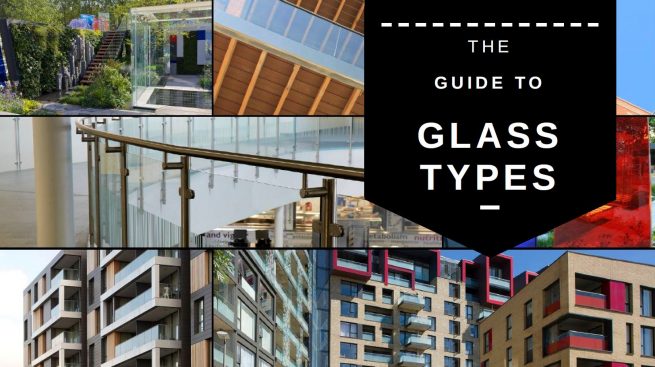
The Float Process was invented by Sir Alastair Pilkington in 1952, allowing larger and more consistent panels of glass to be manufactured than ever before. 64 years later, there are now 260 float plants worldwide which produce glass panels up to 3 metres in width and between 0.4mm and 25mm thick. These plants, which can be up to 1 kilometre long, produce a combined output of about 800,000 tonnes of glass a week!
The ultimate strength of glass is related to the rate at which it is cooled. There are four main types or strengths of glass:
1) Annealed Glass
Annealed glass is a basic product formed from the annealing stage of the float process. The molten glass is allowed to cool slowly in a controlled way until it reaches room temperature, relieving any internal stresses in the glass. Without this controlled slow cooling, glass would crack with relatively little change in temperature or slight mechanical shock. Annealed glass is used as a base product to form more advanced glass types.
2) Heat Strengthened Glass
Heat Strengthened Glass is semi tempered or semi toughened glass. The heat strengthening process involves heating annealed glass back up to about 650 to 700 degrees Celsius and then cooling it quickly, although not as fast as with toughened glass. The heat strengthening process increases the mechanical and thermal strength of annealed glass, making it twice as tough as annealed glass.
When it breaks the fragments are similar in size to annealed glass, but with a greater likelihood of staying together.
This glass is not often used in balustrades or similar structural applications because of its limited strength compared to tempered or toughened glass, although is sometimes specified when there is concern about tempered glass fracturing into thousands of small pieces.
3) Tempered or Toughened Glass
This is the most common type of glass used in balustrades or similar structural applications. Annealed glass is heated to about 700 degrees Celsius by conduction, convection and radiation. The cooling process is accelerated by a uniform and simultaneous blast of air on both surfaces. The different cooling rates between the surface and the inside of the glass produces different physical properties, resulting in compressive stresses in the surface balanced by tensile stresses in the body of the glass.
This process makes the glass four to five times stronger and safer than annealed or untreated glass.
The counteracting stresses or surface compression gives toughened glass its increased mechanical resistance to breakage, and when it does break, causes it to produce small, regular, typically square fragments rather than long, dangerous shards that are far more likely to lead to injuries.
4) Laminated Glass
Any one of the above types of glass can be laminated. The most commonly used finished product is two sheets of toughened glass, laminated together with a 1.52mm thick Polyiynil Butyral (PVB) interlayer.
Laminated glass offers many advantages. Safety and security are the best known of these, so rather than shattering on impact, laminated glass is held together by the interlayer. This reduces the safety hazard associated with shattered glass fragments, as well as, to some degree, the security risks associated with easy penetration.
If a glass panel breaks or shatters it is highly unlikely that both laminated panels will break at the same time, which means that the remaining panel and interlayer will support the broken glass and keep it in place as edge protection until it is replaced or secured suitably.
Another increasingly common interlayer is the SGP Interlayer. The product offers 5 times the tear strength and 100 times the rigidity of standard PVB. In the unlikely event of both panes of toughened glass breaking then the SGP will, in most applications, hold the glass in place. SGP offers an enhanced impact performance and greater protection against severe weather.
A variety of other interlayers are available which apply a range of other technologies to the application. Structural interlayers can be used to enhance the strength of the glass where high loadings are required. Coloured interlayers can be used for privacy or purely decorative purposes. Other properties such as sound dampening and fire resistance can also be incorporated into the interlayer.
BA Systems procure and install in excess of 350 tons of toughened glass per year. Further details on glass are readily available from BA Systems, including glass thicknesses and fixing details when incorporated into balustrade systems. BA Systems manufactures the B20, B30 and B40 balustrade systems using a number of different types of glass types. You can find out more about our systems on this page here.
Back to blog