We provide certainty in an ever-changing world.
Certainty based on innovation and experience.
A programme of continuous development ensures our range of products and services are always compliant with the latest legislation and building requirements.
Our commitment to you
Our internal management systems ensure clear and manageable communication, as we respond to your queries and keep you updated on progress.
We can guarantee our processes and procedures enable us to collaborate intelligently with you and all relevant project personnel to ensure that your project is completed smoothly and successfully.
Our procedures prevent any difficulties for your project team and enable us to synchronise with other contractors. We respond swiftly to any issues that arise and avoid unnecessary project delays.
Our designs comply with all the relevant standards. We offer full structural calculations as part of our package, where applicable.
We do our utmost to ensure your project is delivered and fitted by the agreed deadline. We achieve this time after time by managing our workflow effectively.
We provide the necessary operations and maintenance manuals so you are fully informed on the correct process for your project. Our internal business systems also provide comprehensive client support, guaranteeing a swift response to any queries or site issues.
Corporate Foundation
We strive for continuous improvement. Carefully considered principles and procedures ensure our innovative range of UK designed and manufactured products create safer spaces and enhance living experiences.
Mission
Our mission is to enhance the stability and quality of life through innovation, care and optimism.
Vision
- Through design innovation and skilled fabrication, we aim to be the UK’s No.1 manufacturer of barrier systems.
Values
We aim to enhance the stability and quality of working relationships through:
We are committed to continuous assessment and improvement of the way we work, and the products and services we offer.
While respecting both customers and suppliers alike, we are committed to company and team loyalty. We care about everything we do.
We have an optimistic outlook, always looking for positive resolutions to challenges.
With over two decades’ experience in the design and manufacture of high-quality handrail, balustrade and barrier systems; we have the knowledge and expertise to provide quality British made products, produced on-time and on-budget.
Our people
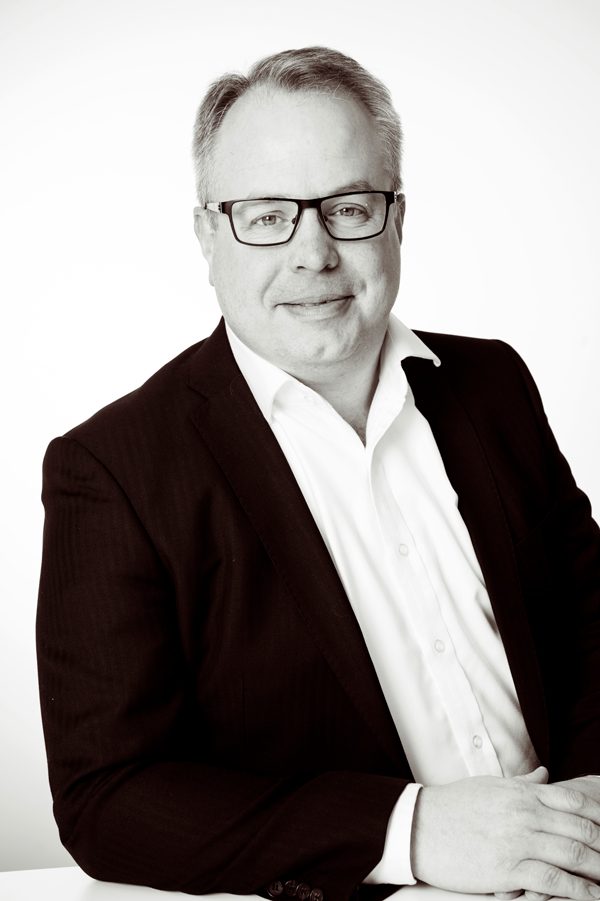
Jim has over 20 years of experience in business development and project management roles, within the Construction Industry. His understanding of client needs allows him to offer practical and cost-effective solutions to clients on a variety of projects across the UK. This allows him to relentlessly qualify and secure new business opportunities to further the company strategic growth goals.
Follow on LinkedIn Email Jim Deans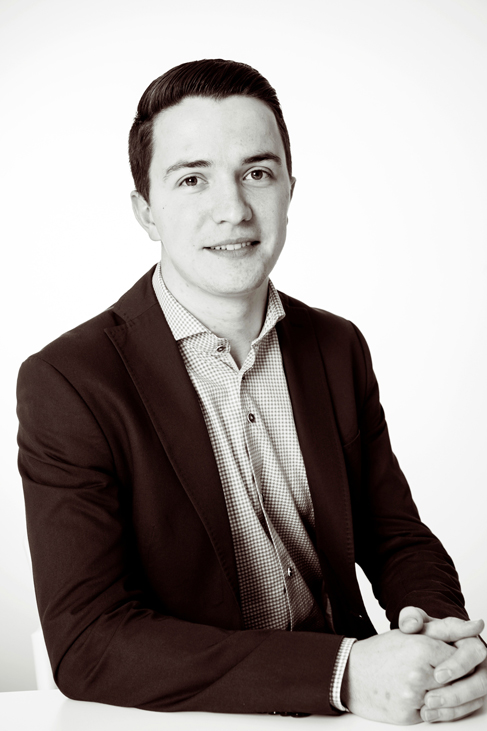
Ben currently has responsibility for overseeing all Sales and Marketing activities for the company. From lead generation to sales strategy, and from managing website presence to coordinating business development campaigns, Ben’s enthusiastic drive makes him the ideal candidate for the implementation of the BA Systems sales and marketing vision.
Follow on LinkedIn Email Ben Hynd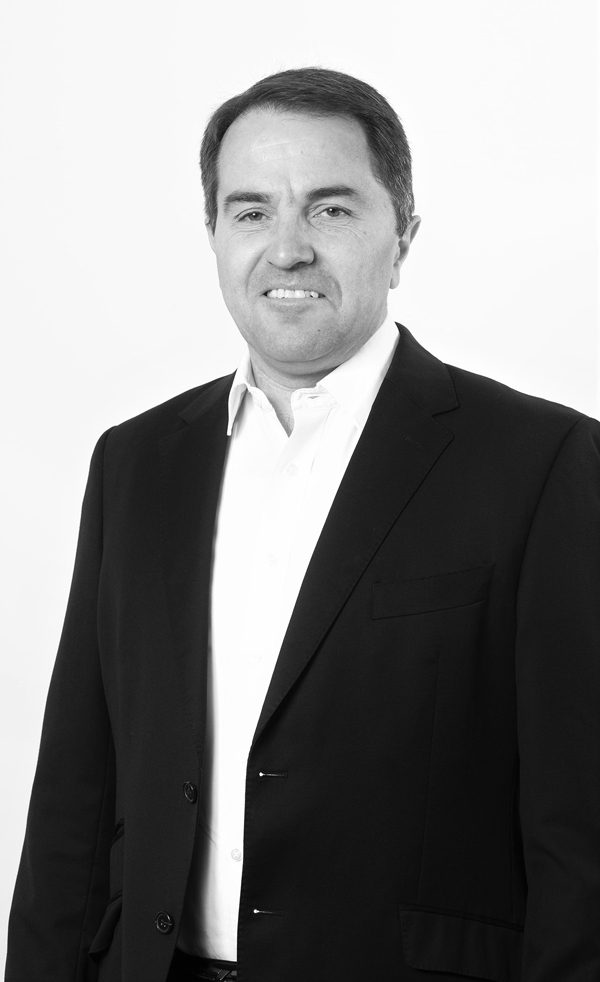
Stephen moved from South Africa and co-founded Brass Age Limited, now trading as BA Systems. With over 25 years’ experience in the industry, Stephen consults the team on the best approach to challenging scenarios. His technical knowledge allows him to develop innovative and bespoke solutions to customer challenges.
Follow on LinkedIn Email Stephen Hynd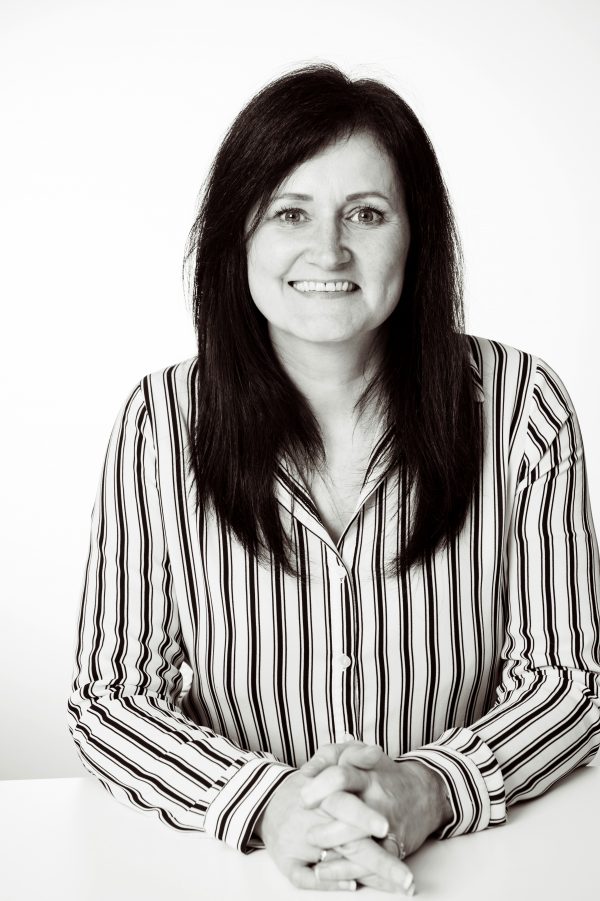
Vicki is responsible for the handover of newly secured projects from sales to operations. In regular communication with customers, Vicki coordinates the receipt of enquiries and the return of quotations. Her busy schedule also includes coordination and project management duties on any after-sales and customer care enquiries.
Follow on LinkedIn Email Vicki Taylor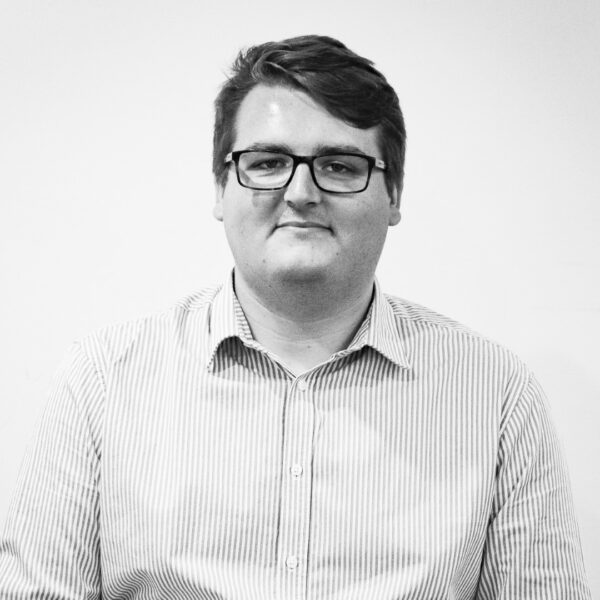
With over 5 years of experience in the construction industry, Rowan is responsible for estimating within the pre-construction department at BA Systems. His knowledge and understanding of projects based business allow him to successfully develop innovative and bespoke solutions for our clients.
Follow on LinkedIn Email Rowan Eastell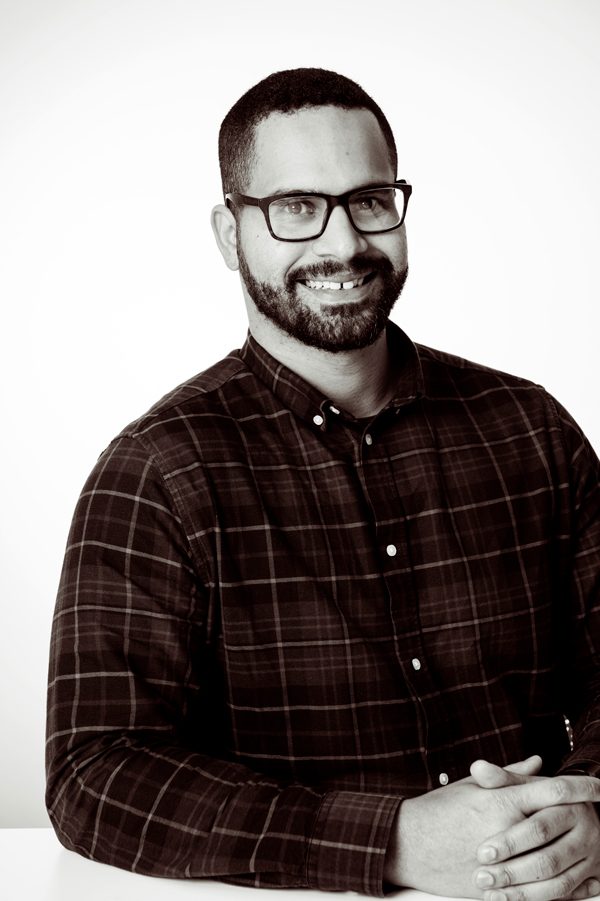
Nicholas has extensive experience in design and engineering, making him an asset to the design team at BA Systems. He manages designs for customer approval, creates drawings for manufacture, coordinates with structural engineers and other related stakeholders. This ensures that flaws are eliminated and challenges on site are minimised.
Follow on LinkedIn Email Nicholas Gurney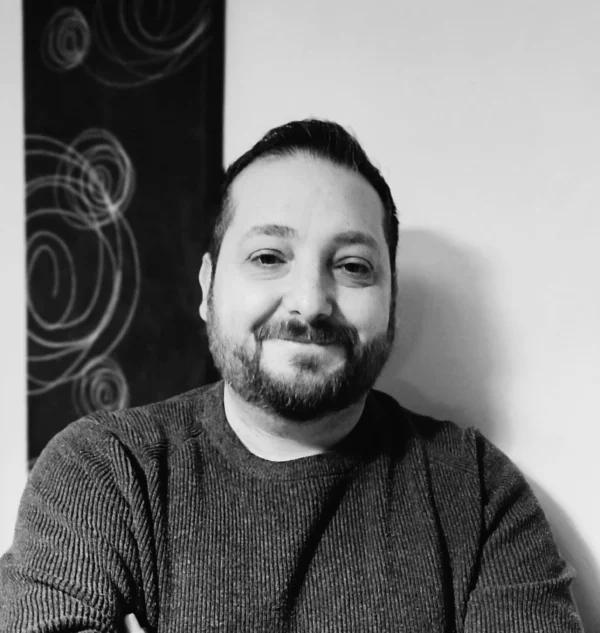
With over 10 years’ experience in CAD and design, Giuseppe’s role includes fabrication drawings as well as managing design for customer approval. Coordinating with structural engineers, architects and related sub-contractors, Giuseppe ensures designs are practical whilst maintaining the quality expectations.
Follow on LinkedIn Email Giuseppe Giriano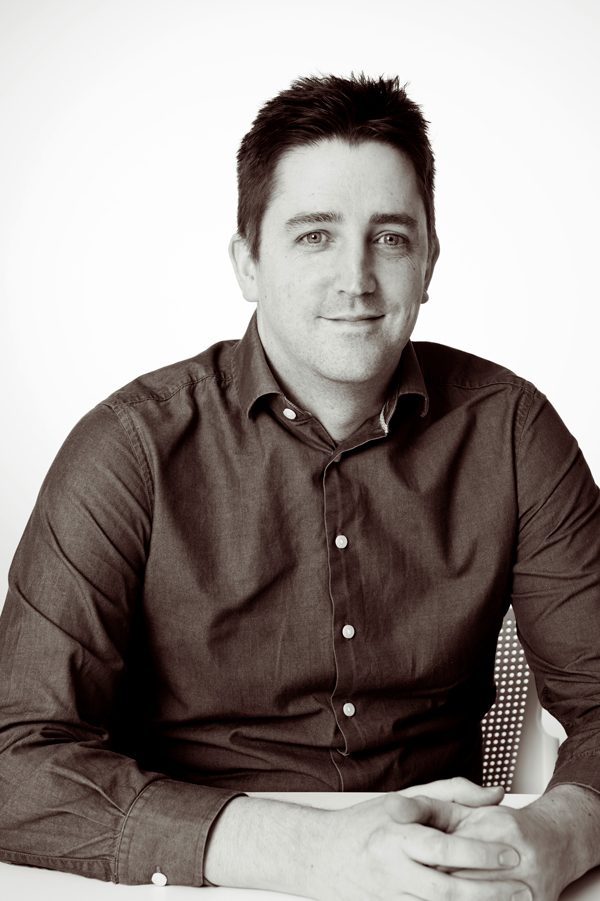
With over 10yrs of experience in the Construction and Metal Fabrication Industry, Darryl’s role sees him managing design for customer approval. His ability to coordinate with structural engineers, architects and related sub-contractors, ensures that designs are both practical and meet safety standards and regulations. This proactive collaboration minimises potential site challenges later in the project.
Follow on LinkedIn Email Darryl Snipe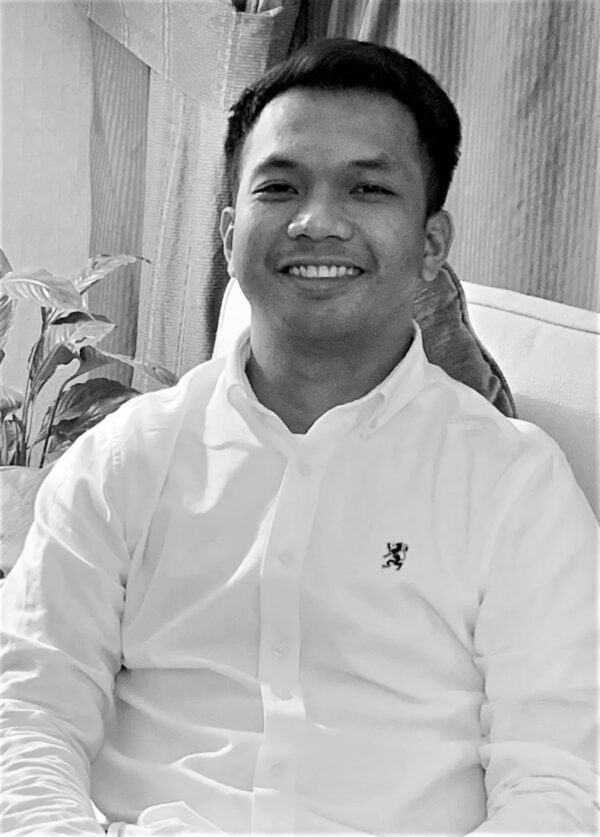
With over 9 years of experience with solid works and working on balustrade design for over two years, Jaypee's role sees him managing designs for customer approval, creating drawings for manufacture whilst coordinating with structural engineers and other related stakeholders to ensure all design is executed to the most accurate dimensions and details.
Follow on LinkedIn Email Jaypee Simon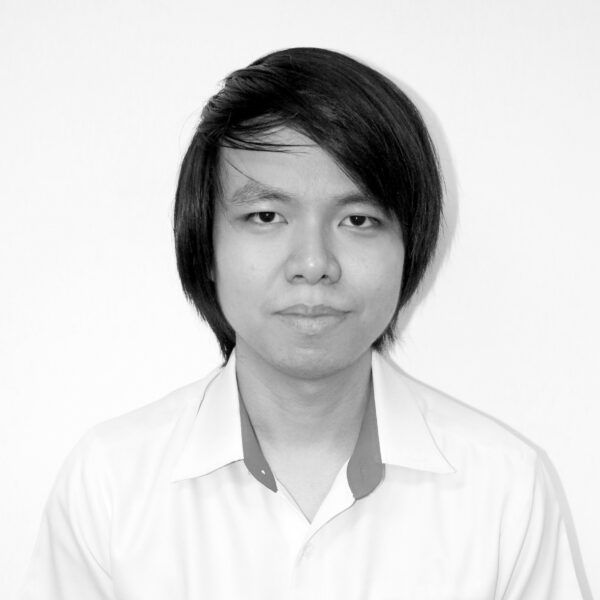
With over 8 years of experience with solid works, Kevin is responsible to manage designs for customer approval and manufacture. Working remotely in the Philippines, he is a valuable asset to the BA team as he seeks to ensure all he coordinates well with the team to produce designs to the highest standard ensuring 100% customer satisfaction at point of project delivery.
Follow on LinkedIn Email Kevin Bon Gelera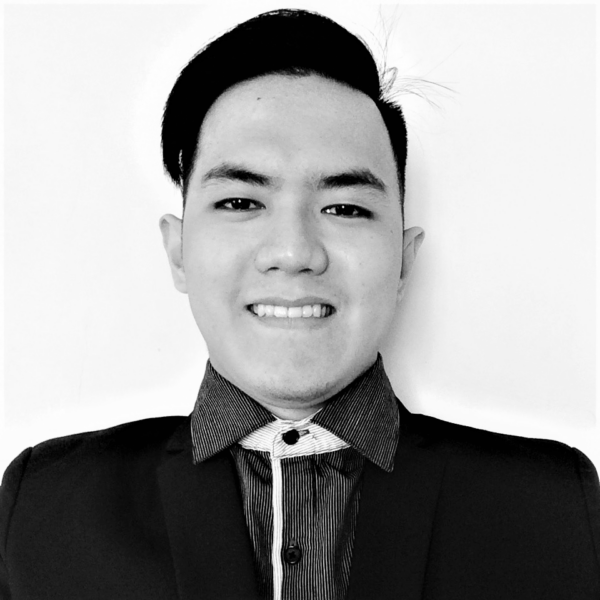
With over 5 years of experience in façade design using both Solidworks and CAD, Seorgino is responsible for coordinating design for customer approval and manufacture. Included in this role is the responsibility to communicate with customers, structural engineers and architects to ensure projects are designed to satisfaction ensuring minimal issues at the point of delivery and installation.
Follow on LinkedIn Email Seorgino Franco Mariano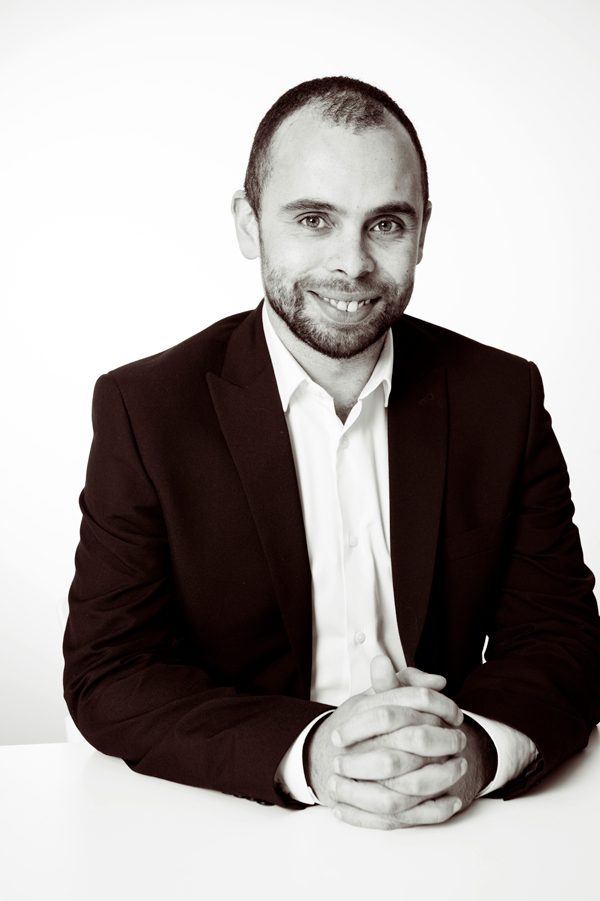
Having over 20 years of experience in varied finance roles and industries, Aedan has helped businesses increase work process efficiency and profitability. His experience in the construction industry as a Finance Manager has proven invaluable in helping lead the modeling, planning and execution of all financial processes within BA Systems. In addition to market trends analysis which has helped the firm generate more revenue and reduce costs, Aedan’s insights have helped highlight key business issues, profit opportunities and potential risks.
Follow on LinkedIn Email Aedan Robinson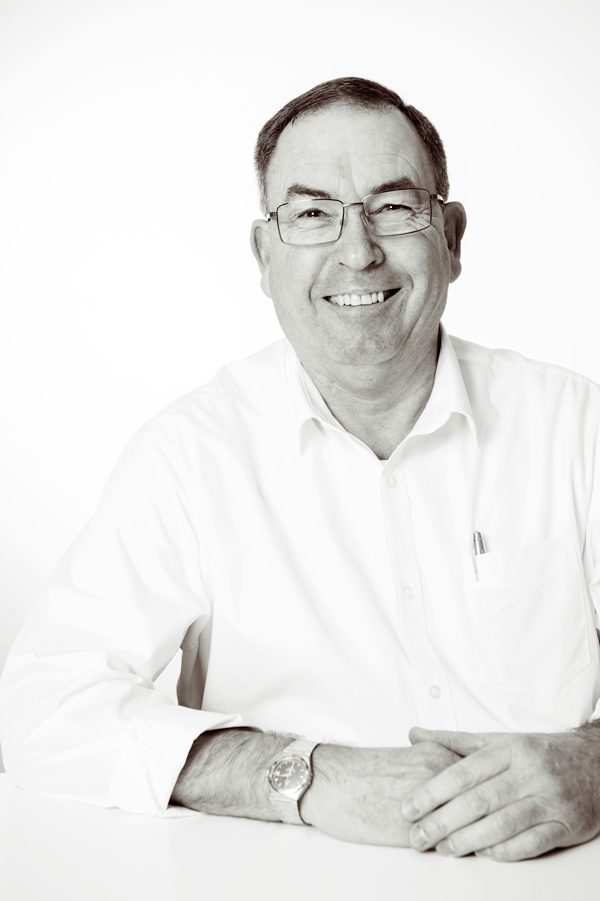
Robert moved from South Africa over 20 years ago and is one of the family co-founders of BA Systems. With over 25 years of experience in the balustrade industry, he is responsible for overseeing the financial status and health of the business, whilst approving and monitoring our contractual documents.
Follow on LinkedIn Email Robert Hynd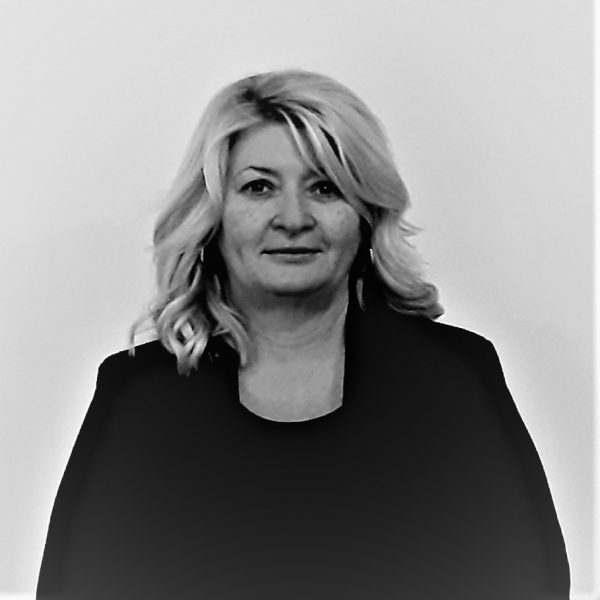
Jackie ensures the smooth running of the finance department by managing the day to day transactions, and being the link between Finance and Operations. Jackie brings over 30 years of experience to BA, and provides strong support to both Aedan and Robert.
Follow on LinkedIn Email Jacqueline Robinson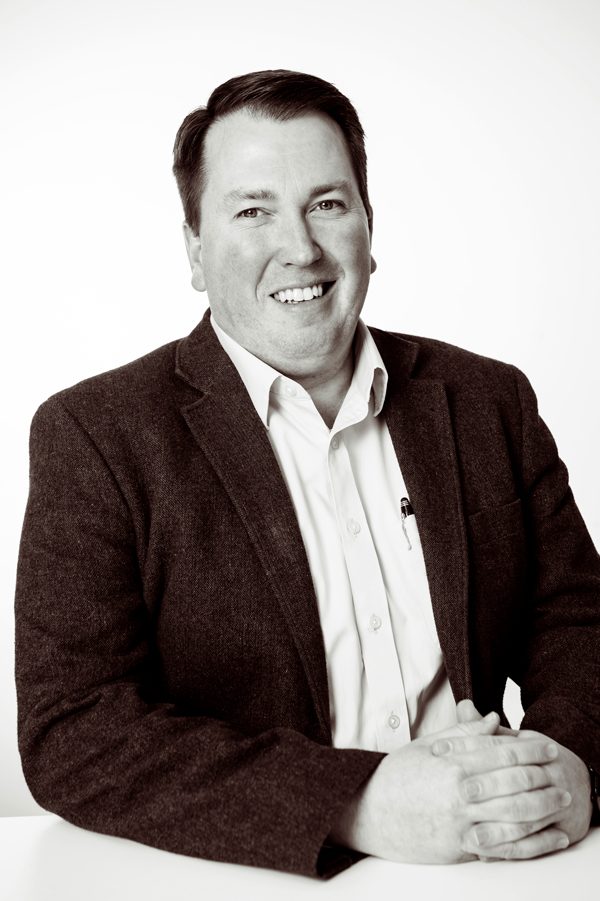
Antony brings more than 25 years of experience in the balustrade industry to BA Systems – which was originally co-founded by him under the name “Brass Age Limited”, after he moved from South Africa. His technical expertise and long-standing experience has proven invaluable in defining the strategic direction and vision of the company. Furthermore, Anthony’s keen business acumen has helped fuel persistent growth and development within the company.
Follow on LinkedIn Email Antony Hynd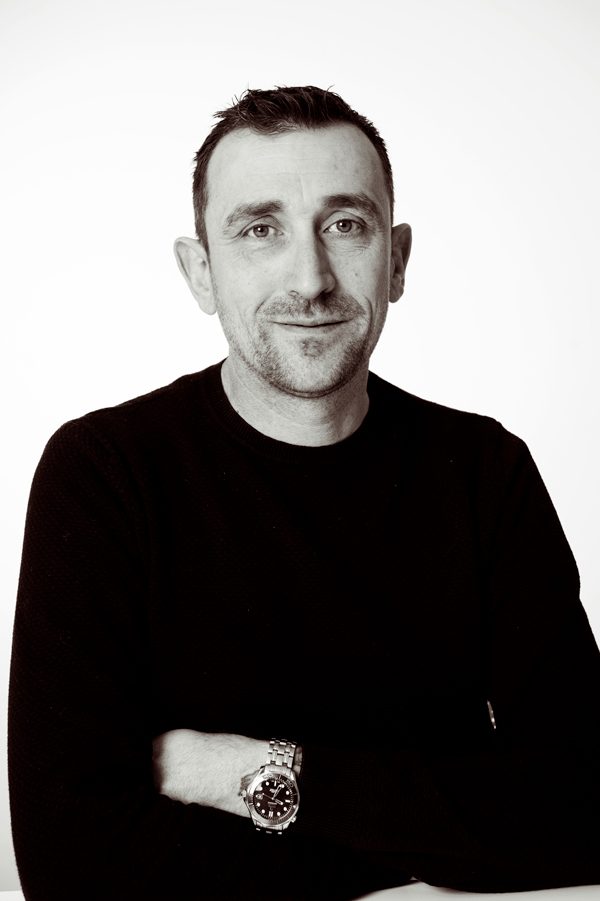
With extensive experience in construction industry and previously employed as a site surveyor, Kevin’s role at BA Systems goes back 7 years. Currently managing and coordinating projects, Kevin has seen many of BA Systems’ largest projects pass through his hands with success. He is currently studying for is NVQ in site supervision and management.
Follow on LinkedIn Email Kevin Sayers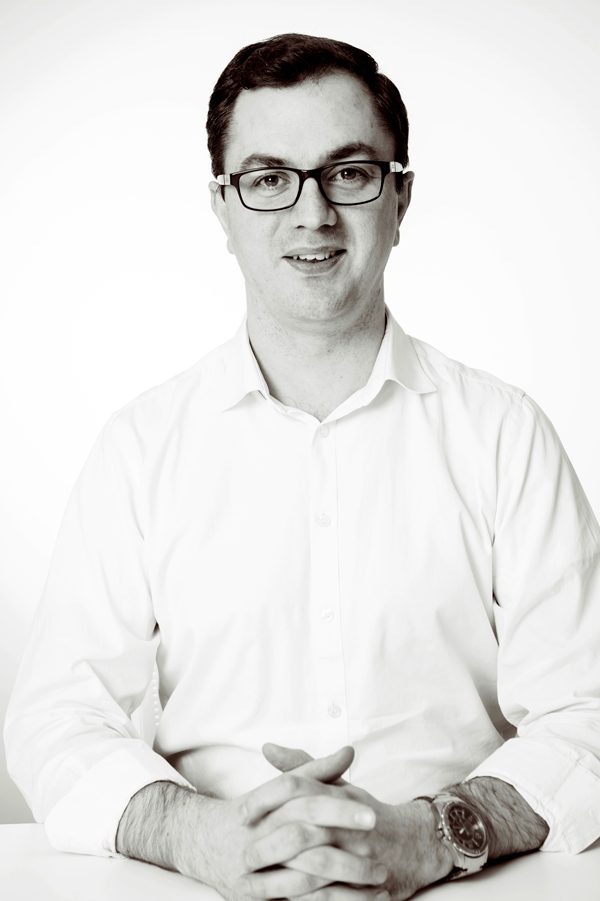
Russell has been with BA Systems for over 17 years with roles involved in fabrication, design and pre-construction. Currently responsible for managing and coordinating the operations team, Russell also manages project flow to ensure quality standards are upheld and project priorities are coordinated. He has worked extensively to promote a culture of lean business processes and systems, striving to continuously improve the entire operational department in line with the Theory of Constraints.
Follow on LinkedIn Email Russell Briston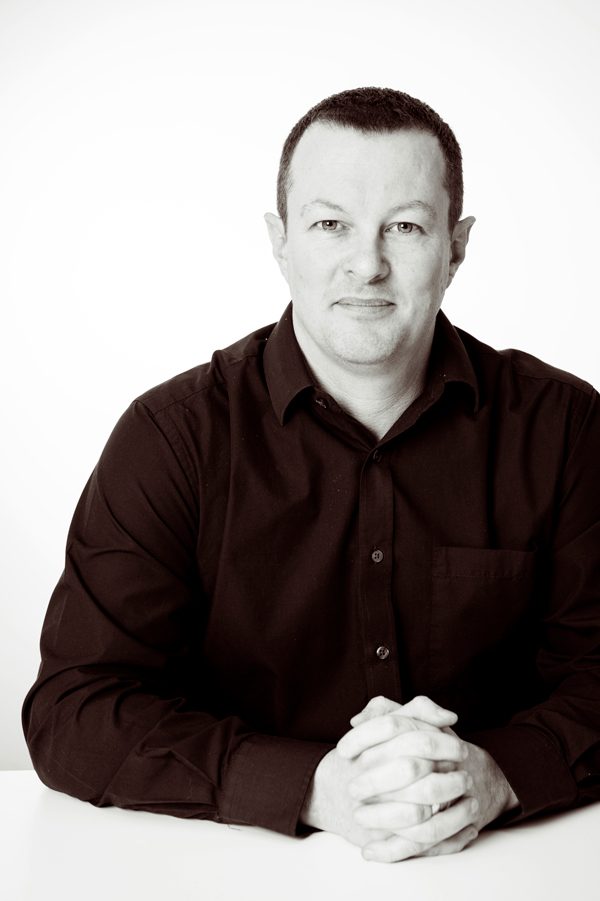
Stephen has been with BA Systems for 5 years and has over 15 years’ experience in varied purchasing roles within the construction sector. His knowledge and experience has helped businesses increase efficiency and profitability through process driven change. Stephen leads both the procurement and manufacturing departments. He is responsible to ensure that the planning and synchronising of goods, services and materials are maintained to client requirements and construction standards. We have found his experience invaluable in driving procedural change, whilst maintaining a solid supply chain to accommodate the growth of BA Systems.
Follow on LinkedIn Email Stephen Smith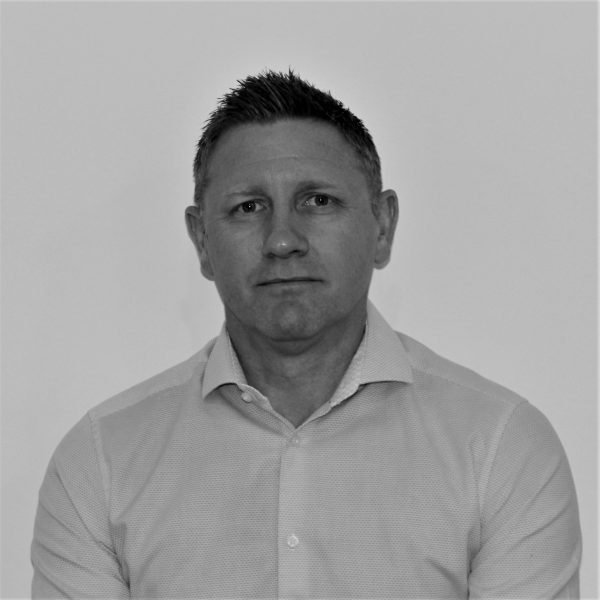
With over 20 years of experience in Project Management within the Construction Industry, Mark is driven to plan, manage and coordinate design at BA. Mark is responsible to oversee the project design team, seeing the importance of a effective and innovative design.
Follow on LinkedIn Email Mark Neave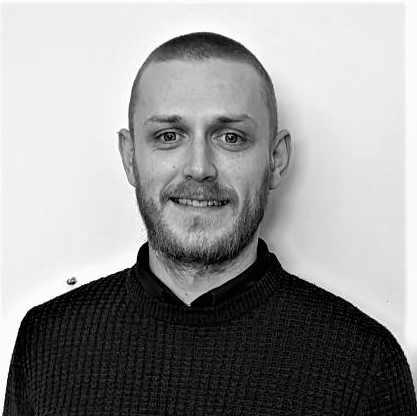
Josh works with our supply chain to deliver materials for projects. In regular communication with suppliers, Josh seeks to ensure the correct quantity of materials are ordered so that we continue to achieve a timely delivery on our projects.
Follow on LinkedIn Email Josh Bone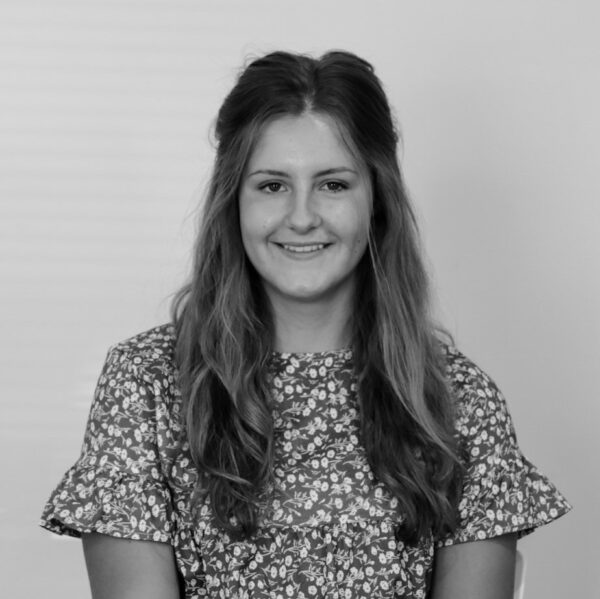
In regular correspondence with our customers, Lucia's role sees her working alongside the Design and Operations team to administratively support the day-to-day flow of design, including managing design submissions, and approvals and coordinating structural calculations with our engineers. Part of her role sees her working alongside the Project Managers to ensure we're aligned with project programs in view of the timely delivery of our projects.
Follow on LinkedIn Email Lucia Goodenough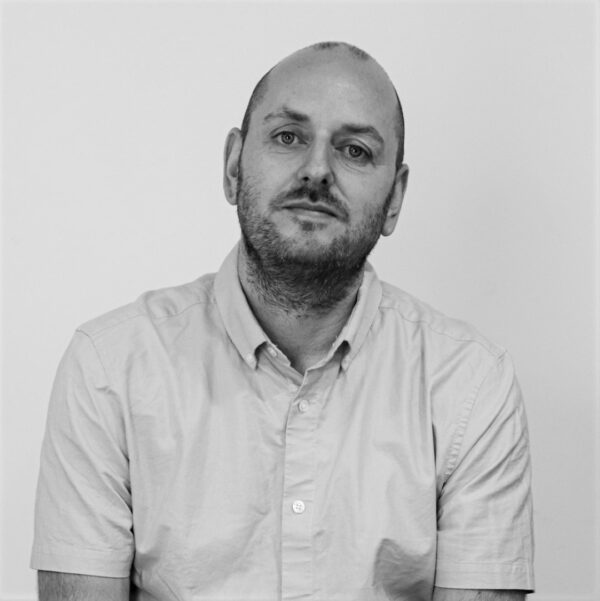
Chris is driven to plan, manage, and coordinate projects at BA. Chris is also responsible for overseeing the project team, seeing the importance of a timely delivery.
Follow on LinkedIn Email Chris Mardell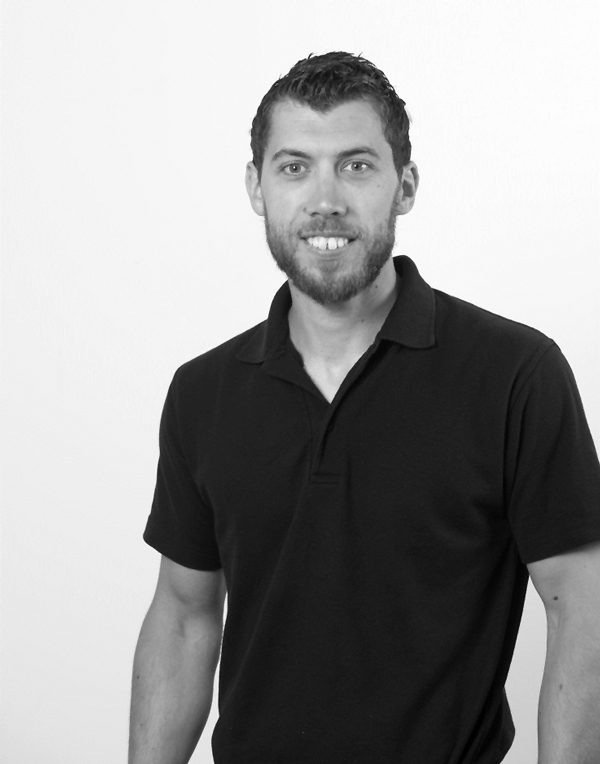
Andrew has been with is for more than 10 years, working in the capacity of a Production Workshop Manager. He has a proven track record in achieving constant improvements in delivery functions, cost and quality. He has also demonstrated the ability to effectively coach and lead a large production team which always accomplishes operational objectives. Seamlessly coordinating all workshop priorities as well as establishing high health and safety standards, Andrew loves developing new processes to improve production accuracy, adding to the firm’s repertoire of quality products.
Follow on LinkedIn Email Andrew Bell
As a workshop operative, Damian’s experience is in welding and supporting the balustrade and handrail fabrication team. Apart from his workshop duties, Damian is also responsible for maintaining stock control and ensuring the timely dispatch of final fabricated product to our sites.
Follow on LinkedIn Email Damian Wojciechowski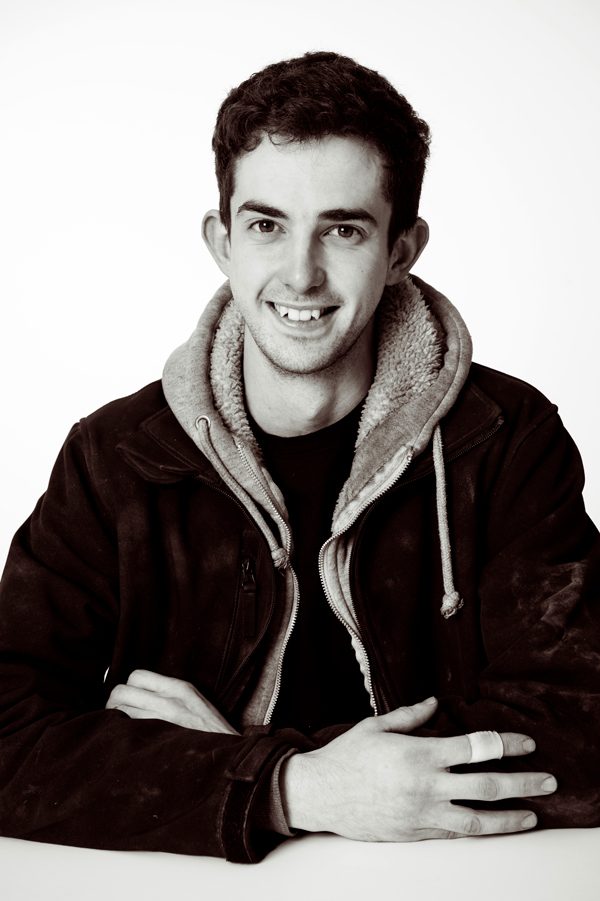
Matthew’s role in the Workshop team, sees him concentrating on the polishing of stainless-steel product and fabrication of the balustrade and handrail systems. Amongst his responsibilities, he also works to ensure there is a timely and efficient dispatch of materials to site.
Follow on LinkedIn Email Matthew Woodgett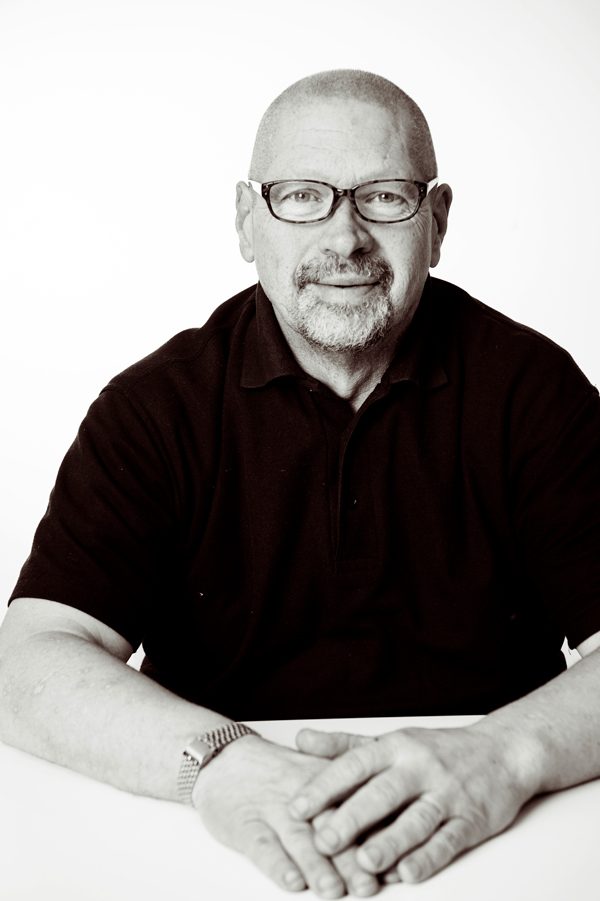
Tommy is part of the workshop team and is responsible for welding and fabrication of stainless-steel balustrade and handrail products.
Follow on LinkedIn Email Tommy Smith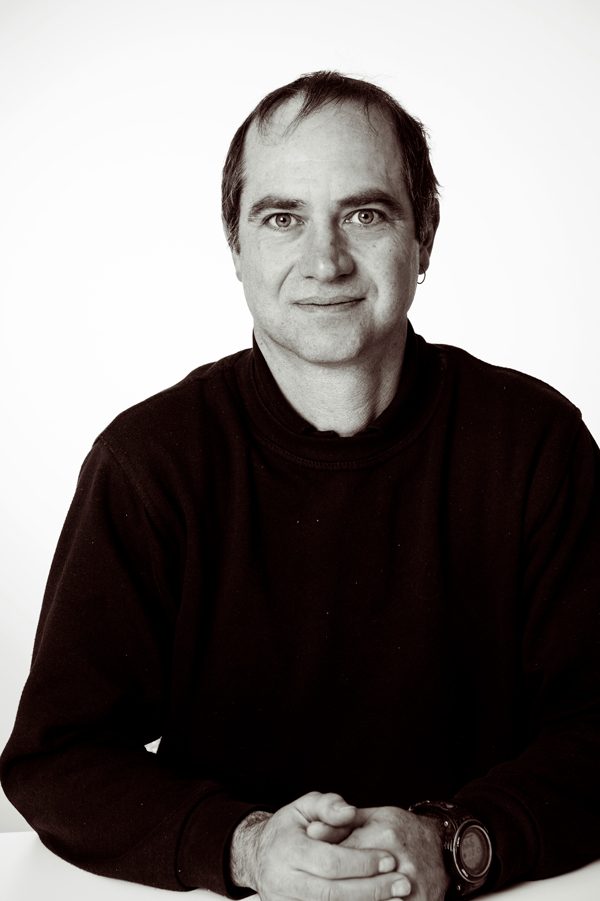
As a member of the workshop team, Phil’s responsibilities are mainly focused on his fabrication duties. He also assists with the smooth and timely dispatch of materials to site.
Follow on LinkedIn Email Phil Cooling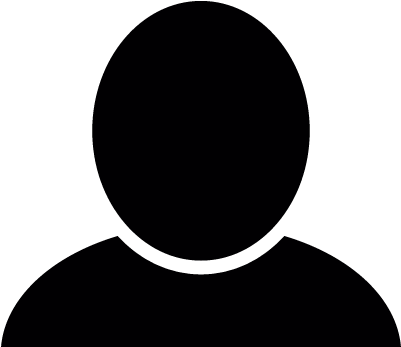
Working predominantly in our Aluminium Workshop, Zane is responsible for the welding and assembly of our aluminium products.
Follow on LinkedIn Email Zane Durant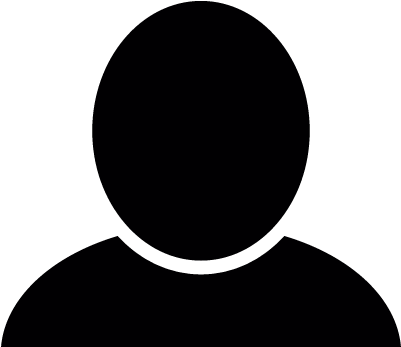
Working predominantly in our Aluminium Workshop, Lulzim is responsible for the welding and assembly of our aluminium products.
Follow on LinkedIn Email Lulzim Jakaj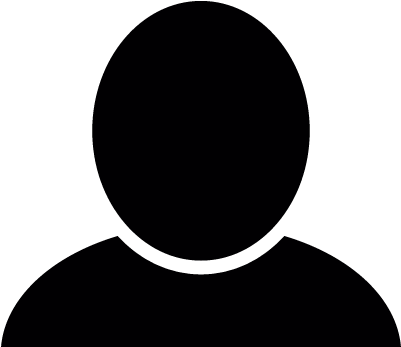
Working predominantly in our Aluminium Workshop, Ben is responsible for the fabrication, including welding and assembly of our aluminium products.
Follow on LinkedIn Email Benjamin Harrison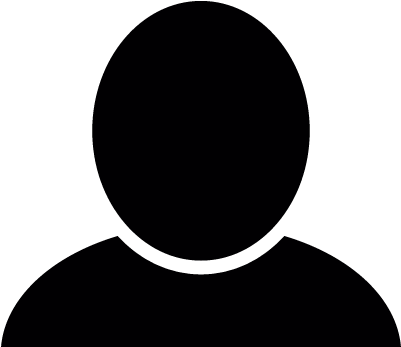
As a member of the workshop team, Daniel's responsibilities are mainly focused on fabrication duties in our aluminium workshop.
Follow on LinkedIn Email Daniel Jakaj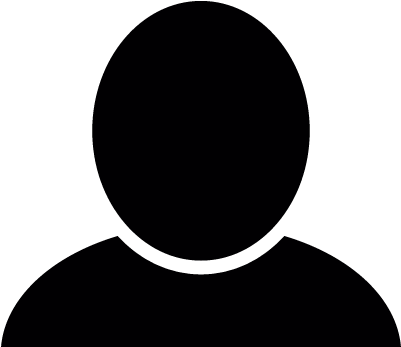
Working predominantly in our Aluminium Workshop, Shaun is responsible for the welding and assembly of our aluminium products.
Follow on LinkedIn Email Shaun Wilson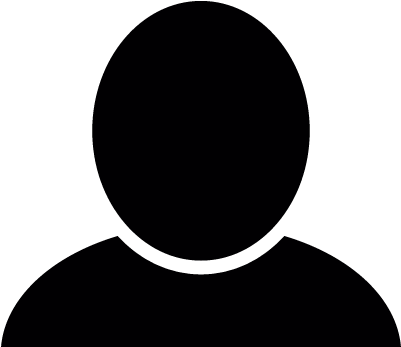
Working predominantly in our Aluminium Workshop, Connor is responsible for the welding and assembly of our aluminium products.
Follow on LinkedIn Email Connor Barrett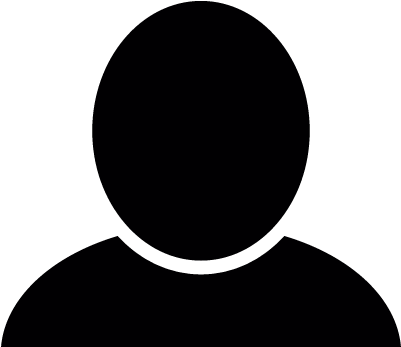
Cole is a member of the Workshop team, where he focuses on his welding and fabrication responsibilities. Neil assists in the coordination and planning of the workshop priorities to ensure that product is fabricated according to site programmes.
Follow on LinkedIn Email Cole ThompsonAssurance
We are proud to have successfully achieved accreditation from, and are fully compliant with the following regulatory bodies.
-
Construction Skills Certification Scheme (CSCS)
-
BSI – in the use of industry-respected best practices
-
Collaboration and sharing of PQQ information
-
A government run scheme to regulate health & safety standards
-
Increasing employment and career prospects of today's youth
-
CQMS health & safety SSIP membership scheme.
-
ISO 9001 and ISO 140001 registered. Certificate Number 16097.
-
The UKCA (UK Conformity Assessment) mark
All these combined means you receive the safest, most professional service possible. See it come together in the BA Systems projects: