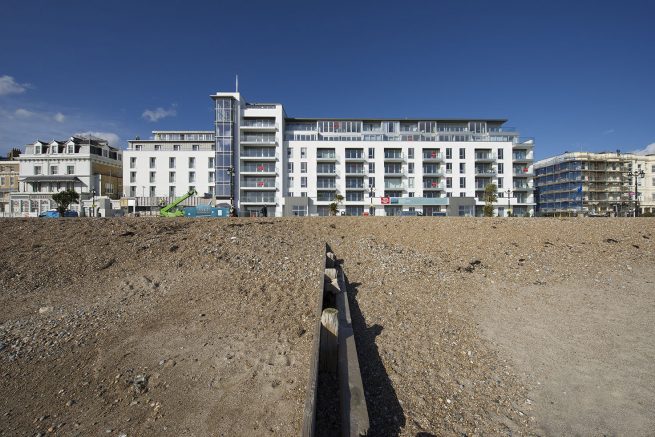
Corrosive Action
Coastal areas and swimming pools are very exacting environments for any construction material including stainless steel. It is important to remember that even 316 marine grade stainless steel with a polished finish is still “stainless” not “stain free” and a regular cleaning regime needs to be implemented. Chlorides from the pool water, salt water and sea air are deposited on the stainless steel and become concentrated by continual wetting from splashing and subsequent evaporation from the surfaces of the metal.
Stainless steel depends for its corrosion resistance on the very thin chromium oxide layer formed on its surface when Chromium is present at 10.5% or above; this is known as the passive layer and the underlying metal is not corrosion resistant. The passive layer forms spontaneously on a clean surface but can be damaged by iron contamination, airborne particles and chlorides in salt water.
Swimming pool environments have changed significantly in recent years, most markedly in leisure pools. Higher water temperatures combined with an increase in the number of bathers, has led to higher levels of chemical disinfection. Chlorine-based disinfectants are the norm, which together with contaminants introduced by bathers, produce chloramines.
The temperature of the air in pool halls is generally held about 1C above water temperature. High air temperatures significantly accelerate corrosion. Atmospheric moisture in pool buildings comes from evaporation of pool water and the droplets from the turbulent water features that have become increasingly common in leisure pools. Higher levels of humidity can lead to condensation in cooler parts of the building and during the cool of the night. Re-circulation of pool air (a common method of reducing energy cost) can increase humidity, as well as adding to the build up of contaminants in the atmosphere.
Consequently, the atmosphere of indoor swimming pools is one of the most aggressive to be found in a building environment and the effects on the material are therefore more significant in the atmosphere than in areas where the stainless steel is continually being washed by pool water.
Corrosion can develop in many different forms but usually manifests itself in tea staining or localised brown stains on the surface which are unsightly and if left untreated can damage the surface of the metal permanently. Tea staining does not normally affect the structural integrity or the longevity of the material and it can be controlled.
Grade 1.4401 (316) stainless steel contains a certain percentage of molybdenum which enhances the corrosion resistant properties of the material and this grade is recommended for these corrosive environments.
Material Finish
Just as critical as the material, is the surface finish. Satin finishes may be aesthetically pleasing but present a micro rough surface with many areas that can be sites for corrosion. The brighter and smoother the surface of stainless steel the less the likelihood of it holding contamination and the greater its corrosion resistance. A smoother surface such as a mirror mechanical polish is therefore most appropriate.
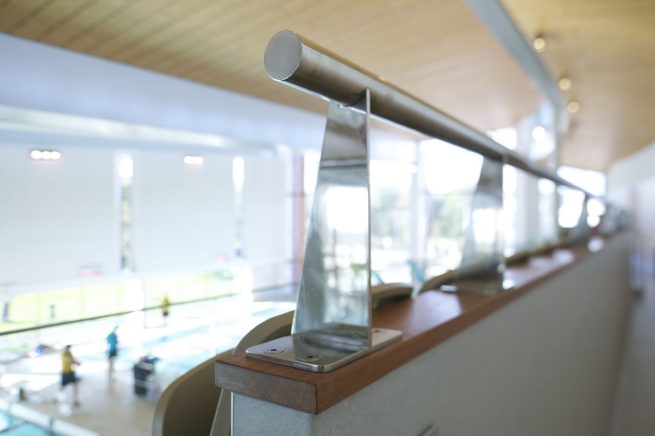
Conclusion and Cleaning Regime
Grade 1.4401 (316) is most appropriate for these corrosive environments but a number of factors need to be considered of which the cleaning and maintenance regime is most important.
The material should be washed on a regular basis with clean fresh water to remove the condensed chlorinated moisture droplets.
Conventional abrasive cleaners or strong acidic cleaners should never be used on stainless steel as this can cause permanent damage to the finish and the metal itself.
It is important to bear this in mind when cleaning brick surfaces adjacent the balustrades. Most brick cleaners contain hydrochloric acid which will cause permanent discoloration of the metal.
To remove heavier soil and salt deposits a mildly acidic water based detergent should be used, diluted with warm water and then rinsed off with clean cold water. If possible the surfaces should be dried off to prevent any water droplet scale forming and to maintain the surface in pristine condition.
By maintaining a regular cleaning program of all the vulnerable surfaces the quality of the metal finish can be maintained for many years.
Back to blog